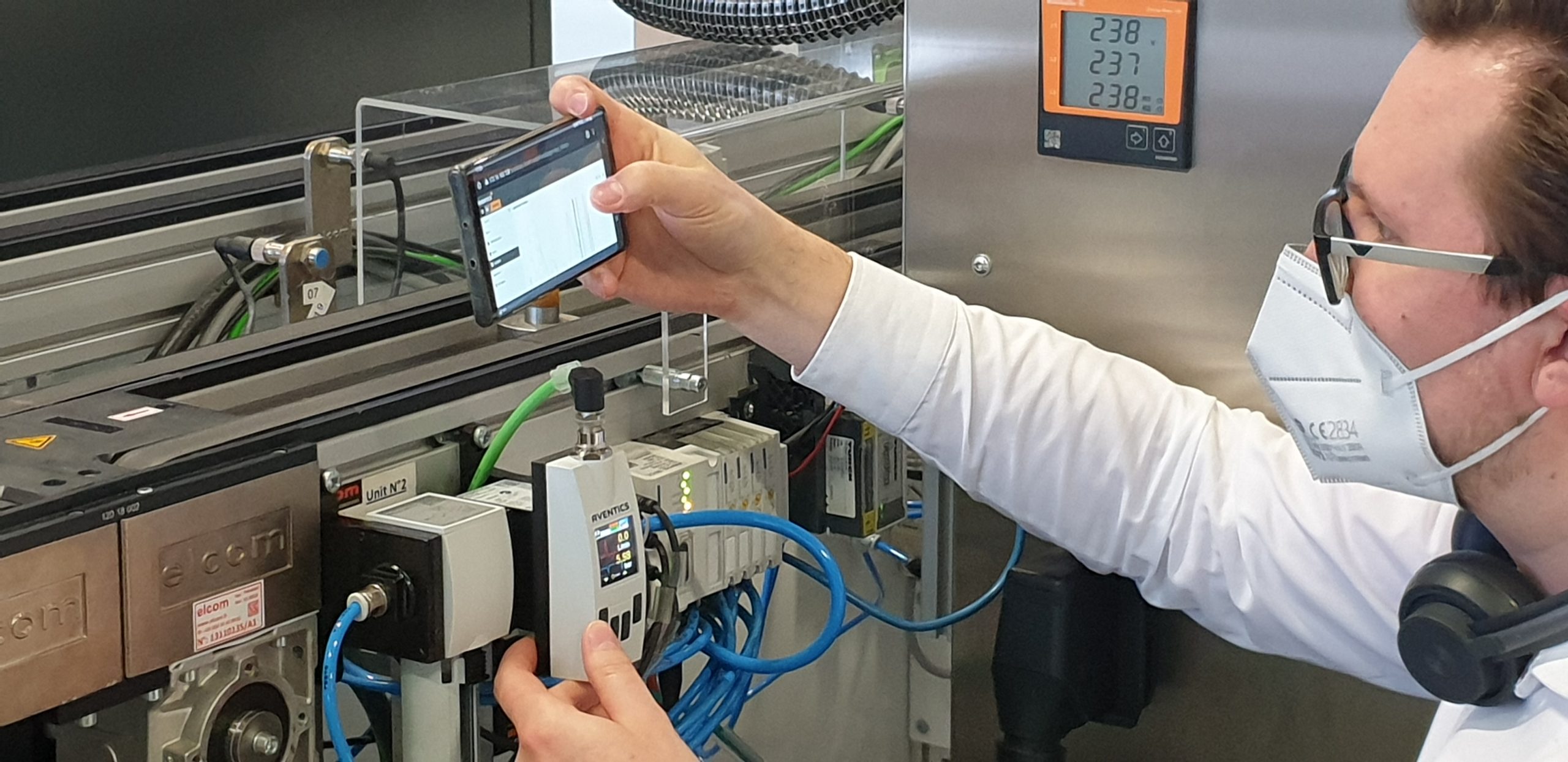
Automatische Leckageverortung unter realen Bedingungen
KI-Anwendungen im Bereich Predictive Maintenance stehen bei vielen Unternehmen als nächster Schritt in der Optimierung des Betriebs von industriellen Produktionsanlagen und Maschinen auf der Agenda. Dabei verspricht der Einsatz von Methoden des maschinellen Lernens viele der zumeist hochgradig automatisierten Prozesse weiter verbessern zu können, um damit spürbare ökonomische Mehrwerte zu generieren.
Für eine erfolgreiche Bewältigung der damit verbundenen, zum Teil erheblichen technischen Herausforderungen, sind die Integration mit den Daten aus dem Shopfloor sowie die Verfügbarkeit passender Lösungsbausteine in einer geeigneten unterliegenden Plattform zur Automatisierung wesentliche Erfolgsfaktoren. Eine andere, essentielle Voraussetzung für den erfolgreichen Einsatz von KI-Verfahren ist deren Erprobung unter realen oder weitgehend realistischen Bedingungen.
Genau dies ist die Zielsetzung des KI Reallabors in der SmartFactoryOWL in Lemgo: Hier können Prozesse rund um Industrie 4.0 von Unternehmen entwickelt, erforscht und demonstriert werden.
Vom virtuellen Hackathon zur realen Anlage
Als einer der weltweit führenden Hersteller von pneumatischen Druckluftventilen veranstaltete die, zum Emerson Konzern gehörige, Aventics GmbH gemeinsam mit dem KI-Reallabor, der AI Community OWL und dem Centrum Industrial IT e.V. letztes Jahr einen Hackathon zum Thema der automatischen Leckageverortung. Hier konnte die AIM Agile IT Management GmbH, ein von ihr entwickeltes Smart Machines KI-Verfahren, erfolgreich anwenden und sich damit gegen die Konkurrenz durchsetzen (siehe Erfolgsgeschichte Intelligente Druckluftsteuerung und Leckagendetektion).
Darauf aufbauend wurde das nun begonnene Kooperationsprojekt ins Leben gerufen, dessen primäre Zielsetzung es ist, das Verfahren unter realen Bedingungen einsatzfähig zu machen. Denn während die Daten des Hackathons von einer unter Laborbedingungen betriebenen Testanalage stammten, erfolgt in diesem Fall der Einsatz an einer analog zum industriellen Produktivbetrieb arbeitenden Demonstrationsanlage im Reallabor der SmartFactory.
Die Anlage besitzt entlang eines Förderbandes drei Stopperzylinder, die den Durchlauf von Werkstücken durch die Anlage steuern. Über einen vierten Zylinder werden die Werkstücke entlang einer Hubachse zur automatischen Bearbeitung durch einen Laser in eine Sicherheitskammer gehoben und nach dem Bearbeitungsprozess wieder abgesenkt. Der gesamte Durchlauf eines Werkstücks durch die Anlage nimmt dabei ca. eine Minute in Anspruch.
Eine AES-Steuereinheit übernimmt die pneumatische Ansteuerung der Zylinder. Über eine weitere, IIoT-fähige AES-Einheit können gezielt Leckagen an einzelnen Zylindern remote vorgegeben und somit simuliert werden. Überwacht wird das gesamte Druckluftsystem durch eine zentral positionierte AF2-Einheit, die Durchflussmenge, Temperatur und Druck des Systems erfasst.
Für die Kommunikation der Steuer- und Sensorsignale zwischen Steuereinheit und Prozess kommt das OPC UA Protokoll zum Einsatz und die generierten Daten werden in einer InfluxDB aggregiert.
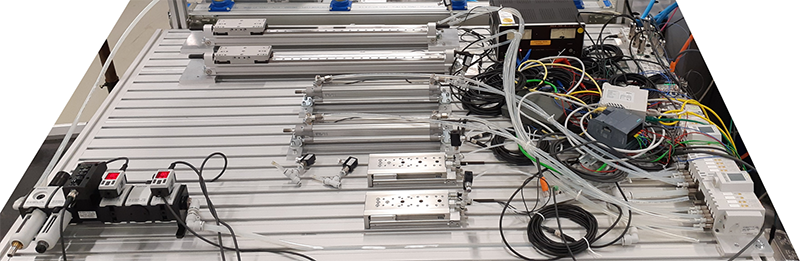
Abbildung: Aufbau Laborversuch (https://www.agile-im.de)
Detektion und Lokalisierung von Leckagen
Zielstellung für das KI-basierte Verfahren ist es, den Zusammenhang zwischen Steuersignalen der Zylinder und dem Messwert für die Druckluft-Durchflussmenge für ein gegebenes Betriebsprogramm zu erlernen. Anschließend kann mit dem Algorithmus die zu erwartende Durchflussmenge vorhergesagt werden. Die Analyse des sich ergebenen Prognosefehlers ermöglicht schließlich die Erkennung und Lokalisierung etwaiger Leckagen. Dabei erlaubt das Verfahren neben der Zuordnung von Leckagen zu einem der Zylindern auch Aussagen über die Zylinderseite (rod/piston) zu treffen, auf der die Leckage vorliegt.
Entsprechend gilt: Je präziser der Algorithmus die Durchflussmenge im Druckluftsystem vorhersagen kann, desto frühzeitiger und robuster kann anhand statistischer Abweichungen des Prognosefehlers eine Erkennung und Verortung von Leckagen geschehen.
Kooperation mit starken Partnern
Seit Anfang des Jahres haben wir uns regelmäßig mit den Projektpartnern via Videochat zusammengefunden, um den Aufbau der Anlage zu spezifizieren und die einzelnen Schritte der Umsetzung zu planen. Dabei konnte dank der guten Zusammenarbeit aller Beteiligten trotz der Corona-bedingten virtuellen Kommunikationskanäle ein zügiger Fortschritt erreicht werden. Nach der regen Planungsphase wird die Anlage derzeit seitens des Fraunhofer IOSB-INA in Zusammenarbeit mit Emerson für die erste Testreihe vorbereitet. Die noch fehlenden Hardware-Komponenten konnten zügig seitens Emerson organisiert und durch das Fraunhofer Institut bereits vor Ort an der Anlage installiert werden.
Wir freuen uns sehr über das Umsetzungsprojekt mit Emerson, AIM und dem CIIT. Das hier praktizierte innovative Zusammenspiel zwischen Komponenten-/Maschinen-Herstellern, praxisnaher Forschung und KI/ML Experten ist ein sehr wichtiger Erfolgsfaktor. Wir hoffen, damit einen wichtigen Schritt in Richtung einer Predictive Maintenance-Lösung für die vollautomatische Erkennung und Verortung von Leckagen in pneumatischen Systemen einer breiten industriellen Anwendungslandschaft zu nehmen. Mit Spannung erwarten wir daher die ersten Ergebnisse.