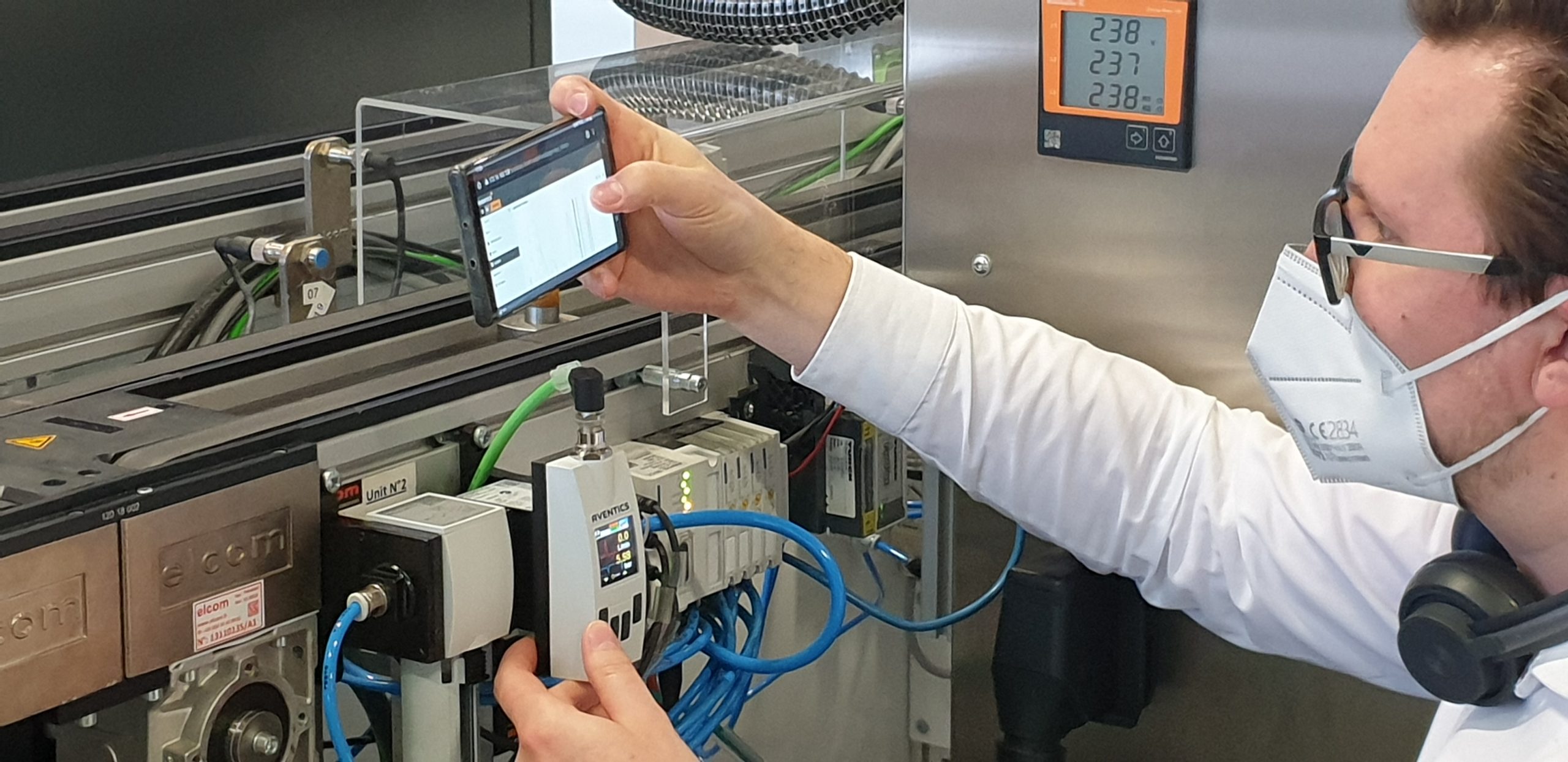
Automatic leakage localization under real conditions
AI applications in the area of predictive maintenance are on the agenda of many companies as the next step in optimizing the operation of industrial production facilities and machines. The use of machine learning methods promises to further improve many of the mostly highly automated processes in order to generate noticeable economic added value.
Integration with data from the shopfloor and the availability of suitable solution modules in a suitable underlying platform for automation are key success factors for successfully mastering the associated, in some cases considerable, technical challenges. Another essential requirement for the successful use of AI methods is their testing under real or largely realistic conditions. Another essential requirement for the successful use of AI methods is their testing under real or largely realistic conditions.
This is precisely the mission of the AI Living Lav of the SmartFactoryOWL in Lemgo: Here, processes related to Industry 4.0 can be developed, researched and demonstrated by companies.
From virtual hackathon to real plant
As one of the world’s leading manufacturers of pneumatic compressed air valves, Aventics GmbH, a member of the Emerson Group, organized a hackathon last year on the topic of automatic leakage localization together with the AI Living Lab, the AI Community OWL and the Centrum Industrial IT e.V..Here, AIM Agile IT Management GmbH, was able to successfully apply a Smart Machines AI process it developed, beating the competition (see success story Intelligent Compressed Air Control and Leakage Detection).
Based on this, the cooperation project that has now begun was launched, the primary objective of which is to make the process operational under real conditions. While the data from the hackathon came from a test installation operated under laboratory conditions, in this case it will be used in a demonstration plant at the SmartFactoryOWL that operates in a manner analogous to industrial production.
The system has three stopper cylinders along a conveyor belt which control the passage of workpieces through the system. A fourth cylinder lifts the workpieces along a stroke axis into a safety chamber for automatic processing by a laser and lowers them again after the machining process. The entire passage of a workpiece through the system takes about one minute.
An AES control unit takes over the pneumatic control of the cylinders. Another IIoT-capable AES unit can be used to remotely specify and thus simulate specific leakages on individual cylinders. The entire compressed air system is monitored by a centrally positioned AF2 unit, which records the flow rate, temperature and pressure of the system.
The OPC UA protocol is used to communicate the control and sensor signals between the control unit and the process, and the generated data is aggregated in an InfluxDB.
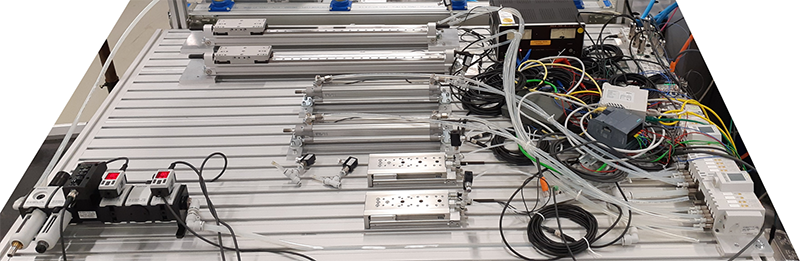
Image: Setup laboratory test (https://www.agile-im.de)
Detection and localization of leakages
The aim of the AI-based method is to learn the correlation between cylinder control signals and the measured value for the compressed air flow rate for a given operating program. Then, the algorithm can be used to predict the expected flow rate. Finally, analysis of the resulting prediction error enables detection and localization of any leaks. In addition to assigning leakages to one of the cylinders, the method also allows statements to be made about the cylinder side (red/piston) on which the leakage is present.
Accordingly, the more precisely the algorithm can predict the flow rate in the compressed air system, the earlier and more robustly leaks can be detected and located on the basis of statistical deviations from the prediction error.
Cooperation with strong partners
Since the beginning of the year, we have met regularly with the project partners via video chat to specify the structure of the plant and to plan the individual steps of the implementation. Thanks to the good cooperation of all participants, rapid progress was achieved despite the Corona-related virtual communication channels. After the lively planning phase, the system is currently being prepared for the first test series by Fraunhofer IOSB-INA in cooperation with Emerson. The missing hardware components were quickly organized by Emerson and installed on site by the Fraunhofer Institute.
We are very pleased about the implementation project with Emerson, AIM and CIIT. The innovative interaction between component/machine manufacturers, practical research and AI/ML experts practiced here is a very important success factor. We hope to take an important step towards a predictive maintenance solution for the fully automated detection and location of leaks in pneumatic systems of a broad industrial application landscape. We are therefore eagerly awaiting the first results.