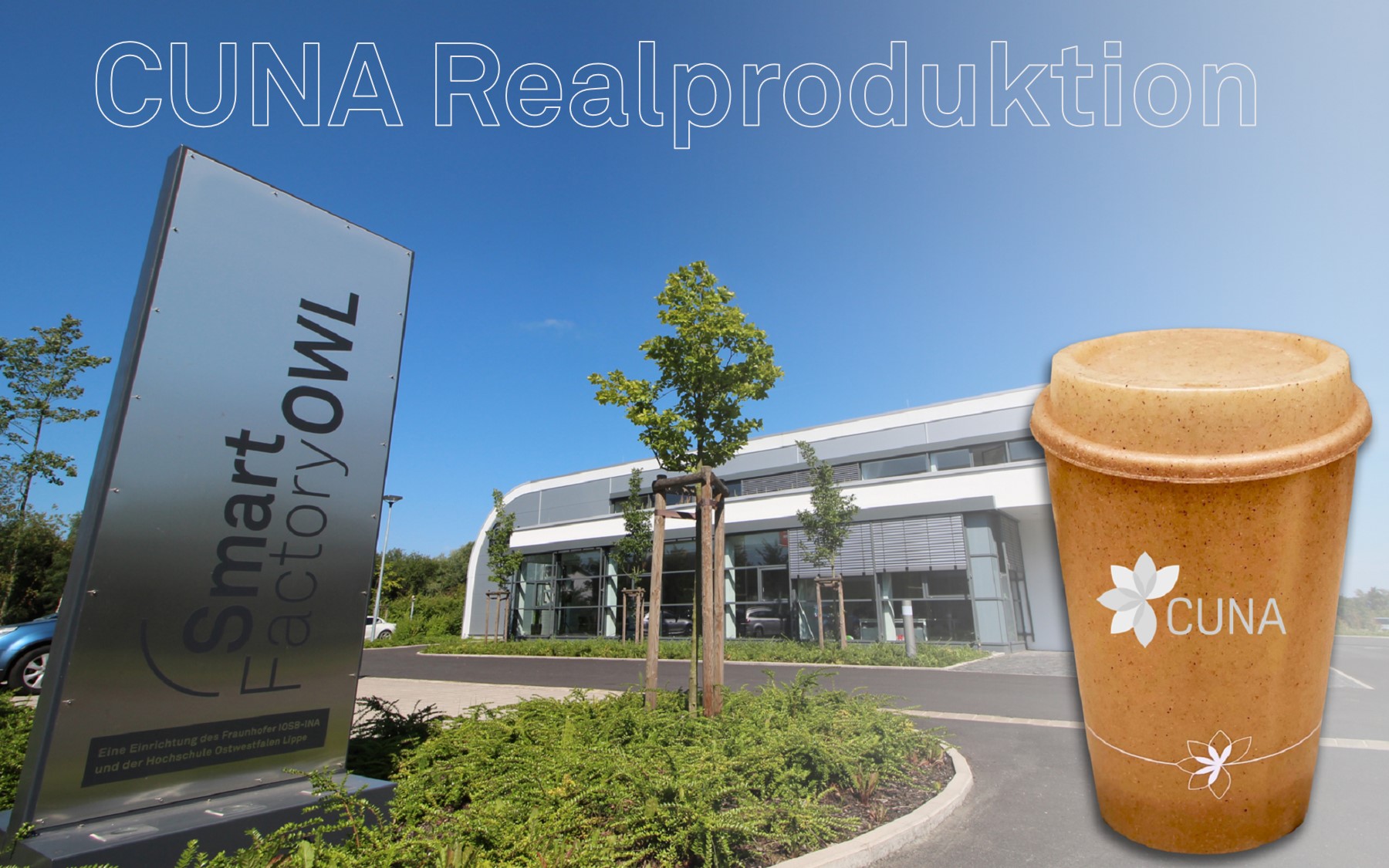
Sustainability and digitalisation – coffee mug unites Germany’s economic goals
Next Level: Fraunhofer IOSB-INA and CUNA start real production in the SmartFactoryOWL
A cooperative of ten partners has formed around the AI Living Lab, funded by the BMWi with 2 million euros, which is jointly developing a digital and sustainable plastics production of the future in the SmartFactoryOWL in Lemgo, in the middle of the top cluster Intelligent Technical Systems Ostwestfalen-Lippe (it’s OWL).
How does the sustainable production of tomorrow work? The product from CUNA – a start-up from Mettmann – shows that technical innovation and environmental protection can harmonise. CUNA Products GmbH produces reusable cups from CO2-neutral, plant-based material. CUNA, founded in 2018, is characterised by a sustainable concept with a future-proof product idea: the cups are made from a bio-based plastic that dispenses with oil and are reusable as well as recyclable. The special feature: not only is the material used for production made from renewable raw materials sustainable, but also the recycling cycle specially organised by CUNA. For this purpose, a material cycle is created through the return flow of used cups of the pool system, because the ecological reusable cups with the distinctive CUNA flower symbol are mainly used as a deposit system in the catering industry or at festivals.
This product also convinced Fraunhofer IOSB-INA, which is researching and implementing the industrial data economy as part of the “AI Living Lab” project funded by the BMWi since the beginning of 2020. In this context, the research institute from Lemgo was looking for production partners to set up real production in the SmartFactoryOWL, a joint initiative of Fraunhofer IOSB-INA and TH OWL. The reason for the search for a real production was, on the one hand, to implement data-driven use cases together with the platform “Industry 4.0” and, on the other hand, to make real industrial data openly available to AI solution providers for the research and development of industrial, data-based solutions. The SmartFactoryOWL has been bringing together companies and research institutions since 2016 to develop and test solutions for the factory of the future in the interaction between man, machine and product and to transfer them into practical application. Real production will also be accessible to visitors to the SmartFactoryOWL.
Now CUNA and Fraunhofer IOSB-INA are setting up data-driven manufacturing in a cooperative of ten partners. They are supported in this by the following corporate partners: The medium-sized plastics processor Hadi-Plast GmbH & Co. KG will take over the production management and operation of the production in the SmartFactoryOWL and will contribute expertise from years of injection moulding production. The overall design and integration of the system technology will be led by the renowned German machine manufacturer ARBURG from Lossburg, which will be flanked by other industrial partners such as the globally active robotics manufacturer KUKA as well as the automation specialists fpt Robotik and Barth Mechanik GmbH. A laser system from REA Elektronik GmbH will be used for the individualised labelling of the CUNA cups. The material supply is organised by the Herford-based medium-sized company digicolor GmbH, which manufactures granulate dryers and colour systems, among other things.
With this fully mapped value chain from the component manufacturer to the production operator to the customer, the production of the sustainable cups is located in the SmartFactoryOWL in Lemgo, in the middle of the technology region OWL, and becomes an experimental field for technologies of Industry 4.0 and artificial intelligence. Fast and agile technology transfer and integration of jointly developed solutions form the basis of the cooperation of this future-oriented production in the SmartFactoryOWL.
CUNA’s founder and CEO Rafael Dyll is proud: “We produce in Germany and from renewable raw materials, reduce CO2 emissions and recycle ourselves. These are all already groundbreaking features. We now want to take the next step and are immensely excited about the cooperation with a world-leading research organisation. At the Fraunhofer Institute in Lemgo, we are also demonstrating that Germany can combine sustainability and digitalisation. And in harmony. In addition, with ARBURG and other partners, we have leading machine manufacturers for plastics production at our side. This constellation of cooperation is unique for research into future bioplastics production, I am sure of that.”
In future, customers will be able to place their orders for CUNA cups online, individualise their products and follow the production of their cups live in the SmartFactoryOWL. The fully digitalised and transparent production continuously provides data for the AI Living Lab. This data is made available to users and developers of artificial intelligence technologies and processes – for example, the simulation company IANUS Simulation, which is also involved in the cooperative – and used to permanently optimise the production processes.
This infrastructure will be used to collaboratively drive the future of the industrial data economy, which the platform Industrie 4.0 aims to strengthen together with Fraunhofer IOSB-INA as part of the AI Living Lab by exploring technologies – with open data, simulations and algorithms.
Nissrin Perez from the SmartFactoryOWL office manages the real production from Fraunhofer IOSB-INA: “The extraordinarily representative and open database via CUNA production in SmartFactoryOWL will mean great progress for German production, especially for the plastics industry. From July, production will start with the set-up in the SmartFactoryOWL.”
Prof. Dr. Jürgen Jasperneite, Director of Fraunhofer IOSB-INA, looks forward to the start with great promise: “We are very pleased that we can now realise a real production in our research and demonstration factory together with the industrial partners. To our knowledge, this kind of “open-heart surgery” is unique in Germany. It places the highest demands on the design of technology transfer during ongoing operations. At the same time, however, this approach offers the fastest maturation process. “
Ernst Stöckl-Pukall, Head of Division IV A 3 – Digitalisation and Industry 4.0 at the Federal Ministry for Economic Affairs and Energy (BMWi) adds: “In Industry 4.0, we are setting global standards with the Industry 4.0 Platform and its network, including the concept for the digital twin. The next step is to put data-driven networking and new business models into practice. This also requires, above all, a willingness to cooperate across companies. The AI Living Lab successfully demonstrates that everyone involved can benefit from this.”