Hannover / Lemgo In pneumatischen Systemen können Luft-Leckagen an den ausführenden und verbindenden Komponenten entstehen, die zu hohen Energieverlusten führen. Die Folge sind ungeplante Stillstände, die mit hohen Kosten verbunden sind. Ad-hoc-Leckagen können direkt vom Fachpersonal erkannt werden – schleichende Leckagen hingegen werden entweder spät oder nicht erkannt. Die herkömmliche Überprüfung erfordert kostenintensive Messinstrumente und entsprechend geschulte Spezialisten, so dass diese meistens (zu) selten oder gar nicht durchgeführt wird. Nicht nur durch die frühzeitige Erkennung, sondern auch die möglichst genaue Verortung solcher Leckagen können also Wartungskosten verringert und ungeplante Ausfallzeiten reduziert werden.
Als einer der weltweit führenden Hersteller von pneumatischen Druckluftventilen veranstaltete die, zum Emerson Konzern gehörige, Aventics GmbH gemeinsam mit der AI Community OWL und dem KI Reallabor am Wochenende vom 27.-29.11.2020 einen Hackathon zum Thema der automatischen Leckageverortung. Hier konnte die AIM Agile IT Management GmbH ein von ihr entwickeltes Smart Machines KI-Verfahren erfolgreich anwenden und sich damit gegen die Konkurrenz durchsetzen (siehe Artikel Intelligente Druckluftsteuerung und Leckagendetektion).
Vom virtuellen Hackathon zur realen Anlage
Darauf aufbauend wurde ein Kooperationsprojekt ins Leben gerufen, dessen primäre Zielsetzung es ist, das Verfahren unter realen Bedingungen einsatzfähig zu machen. Denn während die Daten des Hackathons von einer unter Laborbedingungen betriebenen Testanalage stammten, erfolgt in diesem Fall der Einsatz an einer analog zum industriellen Produktivbetrieb arbeitenden Demonstrationsanlage im Reallabor der SmartFactoryOWL. Genau dies ist die Zielsetzung des Testaufbaus in der SmartFactoryOWL: Hier können Prozesse rund um Industrie 4.0 von Unternehmen entwickelt, erforscht und getestet werden. Im Rahmen der Kooperation zwischen dem Emerson Konzern, dem Fraunhofer Institut für Industrie Automation IOSB-INA und der AIM Agile IT Management GmbH wurde ein Testprojekt rund um die Erkennung und Verortung von Leckagen in pneumatischen Systemen durchgeführt.
Detektion und Lokalisierung von Leckagen
Zielstellung für das KI-basierte Verfahren ist es, den Zusammenhang zwischen Steuersignalen der Zylinder und dem Messwert für die Druckluft-Durchflussmenge für ein gegebenes Betriebsprogramm zu erlernen. Anschließend kann mit dem Algorithmus die zu erwartende Durchflussmenge vorhergesagt werden. Die Analyse des sich ergebenen Prognosefehlers ermöglicht schließlich die Erkennung und Lokalisierung etwaiger Leckagen. Dabei erlaubt das Verfahren neben der Zuordnung von Leckagen zu einem der Zylindern auch Aussagen über die Zylinderseite (rod/piston) zu treffen, auf der die Leckage vorliegt.
Entsprechend gilt: Je präziser der Algorithmus die Durchflussmenge im Druckluftsystem vorhersagen kann, desto frühzeitiger und robuster kann anhand statistischer Abweichungen des Prognosefehlers eine Erkennung und Verortung von Leckagen geschehen.
Herausforderungen/ Aufgabenstellung
Die Konfigurationen von Kundenanlagen sind sehr individuell und bestehen aus wenigen bis mehreren hundert Komponenten. Die physikalischen Eigenschaften (z.B. Viskosität der Luft) und Rahmenbedingungen (z.B. Betriebstemperatur) erlauben keine einfachen linearen Modelle des Gesamtsystems. Häufig stehen in Kundensystemen nur wenige Daten zur Verfügung, da diese bereits älter sind oder Kosten der Sensorik im Verhältnis zu anderen Bauteilen hoch sind. Damit stehen dann lediglich die zentrale Durchflussmenge und die Steuerungsdaten der Anlage zur Verfügung. Damit eine Lösung praxistauglich ist, können zudem keine Trainingsdaten für die eigentlichen Leckagen bereitgestellt werden – sondern nur das aktuelle Referenzverhalten einer Anlage.
Daraus ergeben sich folgende Kernherausforderungen aus Sicht eines für den Praxiseinsatz geeigneten Verfahrens:
- Wenige Signale: bedingt durch fehlende Sensorik
- Heterogenität: individuelle Konfigurationen und Bedingungen der Kundenanlagen
- Komplexität: wenige bis mehrere hundert Komponenten
- Eingeschränkte Trainingsdaten: nur Referenzverhalten
- Nichtlineares Verhalten: physikalische Eigenschaften (z.B. Viskosität der Luft)
- Verortung: Verschleiß muss den Komponenten zugeordnet werden
Insbesondere der letzte Punkt ist anspruchsvoll, da sich die Informationen bezüglich der betroffene(n) Komponente(n) in der Dynamik der Signale „verstecken“.

Abbildung: Schema eines pneumatischen Systems
Projektverlauf und Lösung
Auf Grundlage bisheriger Erfahrungen konnten die Partner früh erste Lösungsideen eingrenzen. Blind Source Separation, um die einzelnen Durchflüsse (Quellsignale) aus dem gemischten Gesamtdurchfluss zu separieren, kam zum Beispiel aufgrund der minimalen Informationslage nicht in Frage. Der zweite – erfolgreiche – Ansatz war, anstelle von konkreten Verschleißorten das Referenzverhalten des Systems zu erlernen. Wenn nun geringfüge Abweichungen vom erwarteten Verhalten auftreten, werden diese frühzeitig vom System erkannt und der verursachenden Komponente zugeordnet.
Wichtig ist aus es für Predictive Maintenance-Lösungen, den technischen Prozess zu verstehen und das entsprechende Domänen-Wissen zu nutzen. Anhand des Testaufbaus erarbeiteten die Partner diese Expertise gemeinsam. Die Testanlage besitzt entlang eines Förderbandes drei Stopperzylinder, die den Durchlauf von Werkstücken durch die Anlage steuern. Über einen vierten Zylinder werden die Werkstücke entlang einer Hubachse zur automatischen Bearbeitung durch einen Laser in eine Sicherheitskammer gehoben und nach dem Bearbeitungsprozess wieder abgesenkt. Der gesamte Durchlauf eines Werkstücks durch die Anlage nimmt dabei ca. eine Minute in Anspruch.
Eine AES-Steuereinheit übernimmt die pneumatische Ansteuerung der Zylinder. Über eine weitere, IIoT-fähige AES-Einheit können gezielt Leckagen an einzelnen Zylindern remote vorgegeben und somit simuliert werden. Überwacht wird das gesamte Druckluftsystem durch eine zentral positionierte AF2-Einheit, die Durchflussmenge, Temperatur und Druck des Systems erfasst.
Für die Kommunikation der Steuer- und Sensorsignale zwischen Steuereinheit und Prozess kommt das OPC UA Protokoll zum Einsatz und die generierten Daten werden in einer InfluxDB aggregiert.
Abbildung: Aufbau Laborversuch
Der Startschuss war erfolgt. In kurzen agilen Sprints ging AIM Schritt für Schritt in enger Abstimmung mit dem Emerson-Team voran. Zu den Erfolgsrezepten gehört der Start jeder Lösungsentwicklung mit einem Data Quick Check – hierbei werden z.B. die Periodizitäten der Steuerung, Latenzen und Synchronität der Steuersignale sowie generelle Auffälligkeiten in den Messreihen, wie Aussetzer oder Ausreißer, analysiert und visualisiert. Bereits bei den ersten Analyse-Ergebnissen sind spannende Erkenntnisse und Diskussionen über den technischen Prozess und Signalübermittlung entstanden, z.B. über Informationsverluste aufgrund geringer Phasenverschiebungen, der Periodenverhältnisse der Schaltfrequenzen und identifizierter Schwankungen und Verschiebungen der Zeitstempel.
Abbildung: Verteilung der Differenzen der Zeitstempel
Mit diesem Wissen ging es weiter in die Entwicklung des Verfahrens, welches erfolgversprechend erschien: Nur auf Basis der Steuersignale wird ein Prognosemodell für den zentralen Gesamtdurchfluss des Systems trainiert. Der entscheidende Trick ist dabei, nicht nur die binären Steuerungsdaten zu verwenden, sondern durch die Generierung zusätzlicher Informationen dem Modell die Systemdynamik einfacher zugänglich zu machen. Das relativ einfache Modell erreicht eine Prognosegenauigkeit von über 90%. Wobei diese tatsächlich nicht der entscheidende Faktor ist, sondern nur dazu dient, einen statistisch signifikanten Prognosefehler zu ermitteln, wenn schleichende Leckagen das Systemverhalten verändern.
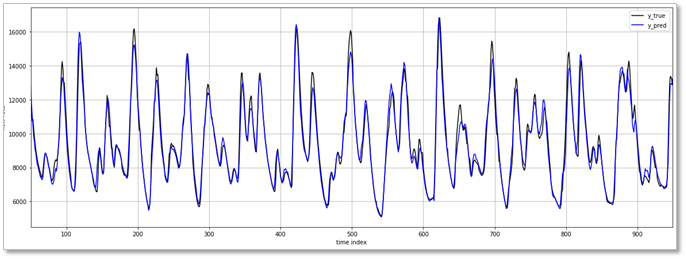
Abbildung: Vorhersage des Luftdurchflusses: Prognosefehler < 10%
Um letztendlich die Leckage zu verorten, erfolgen weitere Analyseschritte und ein Signifikanztest. Dies erfolgt rollierend über konfigurierbare Zeitfenster, so dass eine Folge von Testergebnissen entsteht – im folgenden Beispiel ist die Zuordnung der Leckage klar zu erkennen (durchgehende rote Markierung).
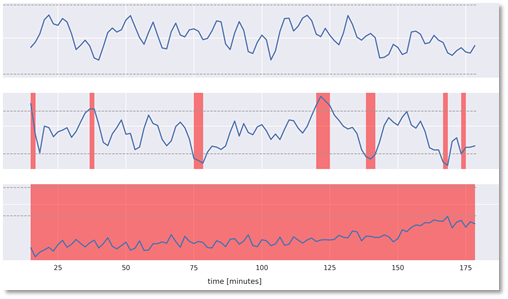
Abbildung: Statistische Signifikanz der zugeordneten Abweichungen über die Zeit
Natürlich ist auch die Datenmenge bzw. -sparsamkeit ein wesentlicher Aspekt: Bereits auf Basis einer kurzen Trainingszeit (Kalibrierung) und binnen weniger Minuten der Prognose (Monitoring) werden Abweichungen erkannt und lokalisiert. Um dies zu erreichen, analysieren wir die Wirkung einerseits verschiedener Kalibrierungszeiträume auf die Leistung und andererseits wachsender Abstand zum Monitoring auf die Stabilität:
Abbildung: Analyse der Kalibrierungszeiträume
Diese Lösung ist ein gutes Beispiel dafür, dass eher nicht die „Brute Force“ Anwendung von KI, welche häufig im Zuge des Hypes z.B. um Deep Learning propagiert wird, zum Erfolg führt, sondern die Kombination von Domänen-Wissen, klassischen Methoden und einfachen Machine Learning-Modellen wesentlich zielführender sein kann.
Bisherige Ergebnisse und Ausblick
Bereits im Proof of Concept und im anschließenden MVP (Minimum Viable Product) ist eine integrierte Gesamtlösung entstanden: Das pneumatische System kommuniziert per MQTT (oder über eine Datenbank) mit dem KI-basierten Verfahren und wird im Modus „Calibrate“ vollautomatisch angelernt. Der Modus „Monitor“ überwacht das System und sendet kontinuierlich einen Leckage Status zu allen Komponenten.
Auf dieser Basis kann die Integration in SPS oder Monitoring Lösungen einfach vorgenommen werden.
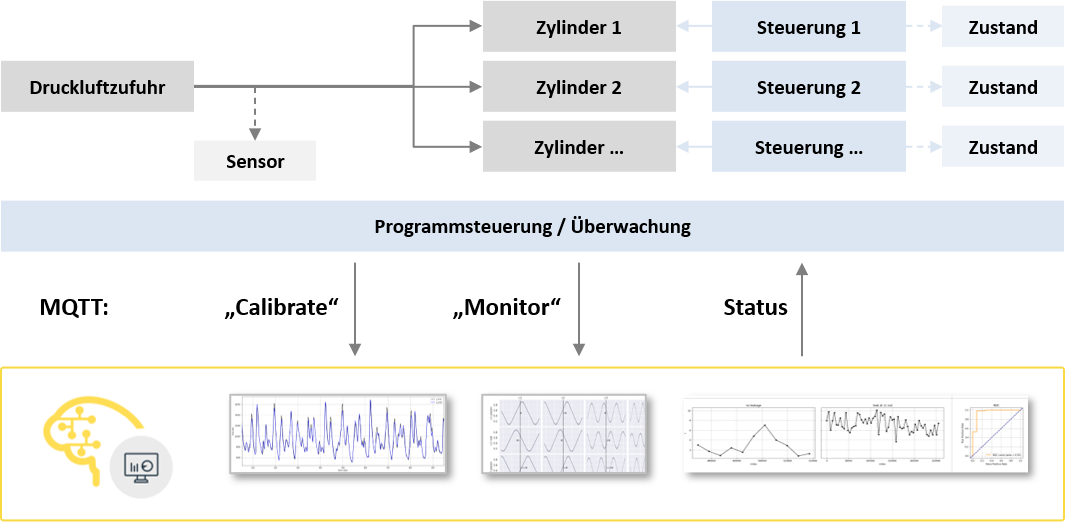
Abbildung: Integrierte Gesamtlösung
In weiteren Schritten wird nun der Komplexitätsgrad kontinuierlich erweitert, um z.B. unterschiedliche Ablaufprogramme, Komponenten und Verbindungen zu verproben – und das Verfahren kontinuierlich zu verbessern und zu erweitern.
Ziel ist es, künftig möglichst viele Kundensituationen abzudecken und in 2021 das Verfahren bei ersten Pilotkunden von Emerson zum Einsatz zu bringen.
Kooperation mit starken Partnern
Dank der guten Zusammenarbeit aller Beteiligten trotz der Corona-bedingten virtuellen Kommunikationskanäle konnte ein zügiger Fortschritt erreicht werden. Nach der regen Planungsphase wurde die Anlage derzeit seitens des Fraunhofer IOSB-INA in Zusammenarbeit mit Emerson und AIM für die erste Testreihe vorbereitet. Die noch fehlenden Hardware-Komponenten konnten zügig seitens Emerson organisiert und durch das Fraunhofer Institut bereits vor Ort an der Anlage installiert werden.
Das AIM Team freut sich sehr darüber, in dieser Kooperation Wissen und Erfahrung im industriellen KI Einsatz einbringen zu können: “Das hier praktizierte innovative Zusammenspiel zwischen Komponenten-/Maschinen-Herstellern, praxisnaher Forschung und KI/ML Experten ist aus unserer Sicht ein sehr wichtiger Erfolgsfaktor. Wir hoffen aus der Kooperation mit diesen hochkarätigen Partnern heraus einen wichtigen Schritt in Richtung einer Predictive Maintenance-Lösung für die vollautomatische Erkennung und Verortung von Leckagen in pneumatischen Systemen einer breiten industriellen Anwendungslandschaft zu nehmen. Mit Spannung erwarten wir daher die ersten Ergebnisse.”