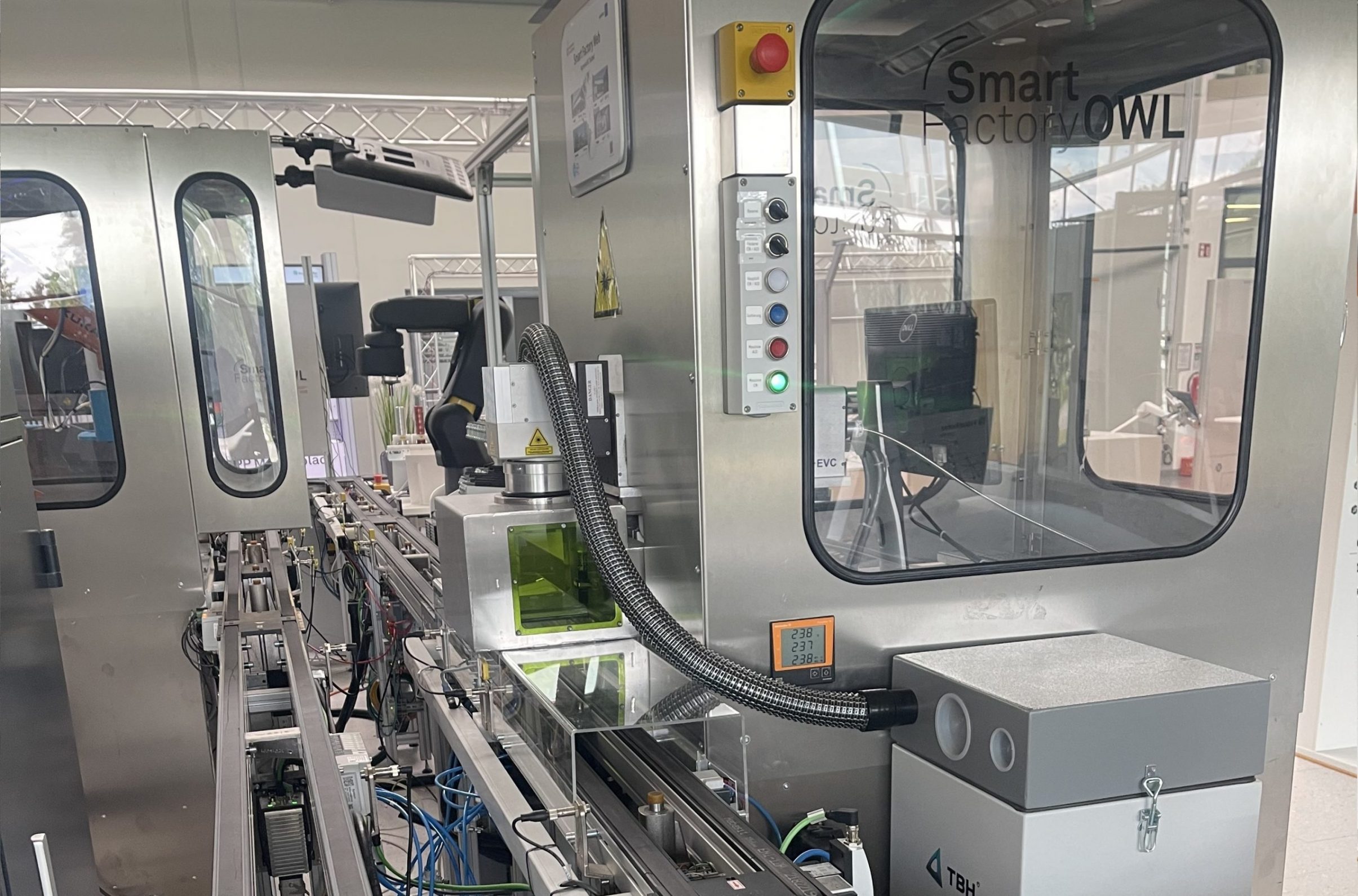
Erfolgreicher Einsatz der automatischen Leckageverortung in der SmartFactoryOWL
Vor wenigen Monaten haben wir in unserem Blog-Beitrag über die “Automatische Leckageverortung unter realen Bedingungen” ein Umsetzungsprojekt vorgestellt, das im Rahmen des vom KI Reallabor, der AICommunityOWL und dem Centrum Industrial IT (CIIT) organisierten Hackathons entstand. In Zusammenarbeit mit den Organisatoren, dem Challengegeber Emerson Solutions und dem Gewinner AIM Agile IT Management GmbH wurden die nächsten Arbeitsschritte hin zu einer Demonstrationsanlage in der SmartFactoryOWL erfolgreich umgesetzt.
Wie bereits im vorherigen Beitrag beschrieben, wurde die über vier Druckluftzylinder verfügende Anlage zunächst um die benötigte Hardware für Sensorik, Steuerungs- und Kommunkationstechnik sowie die Pneumatik zur Leckagesimulation (siehe Abbildung 1) erweitert. Anschließend war das Fraunhofer IOSB INA softwareseitig für einen reibungslosen Betrieb der Anlage verantwortlich. Dies beinhaltete u.a. die Aggregation der Daten (in einer InfluxDB) sowie die Bereitstellung sicherer Zugänge auf die Datenbank für die beteiligten Partner Emerson und AIM. Zusätzlich wurde die Netzwerkkommunikation der Datenpakete optimiert, sodass eine reibungslose Aufzeichnung der Steuer- und Sensorsignale bei vergleichsweise niedrigen und gleichmäßigen Latenzen gewährleistet werden konnte.
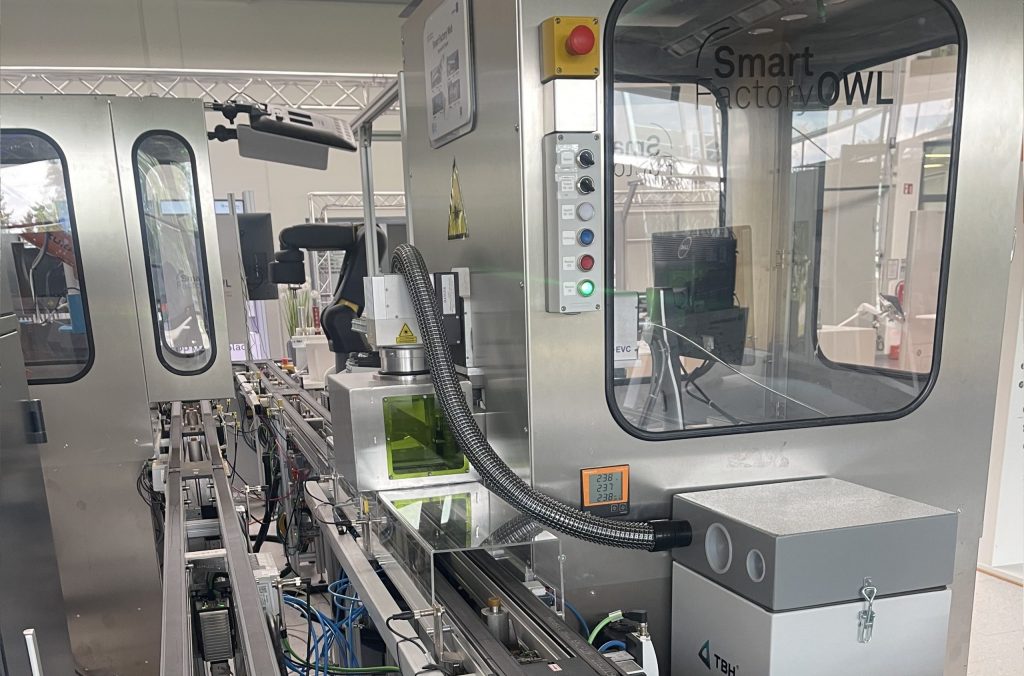
Abbildung 1: Die Demonstrationsanlage mit Förderband und Bearbeitungskabine.
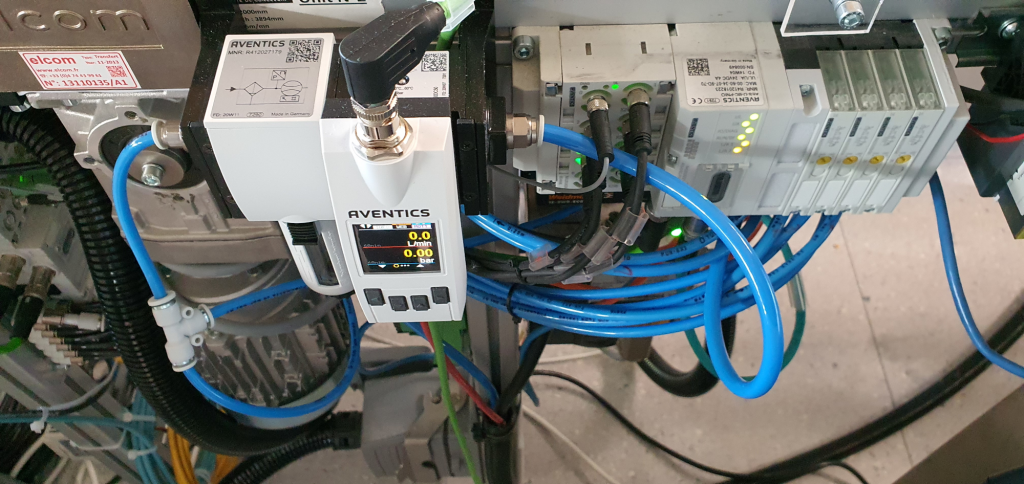
Abbildung 2: Zentrale Sensorik (AF2-Durchflusssensor, mittlere Einheit mit Display)
und Ansteuerungseinheit der Druckluftzylinder (AES, rechte Seite).
Von der Datenanalyse zur Anwendung des Verfahrens
Aufgrund dieser Vorarbeiten konnten im Mai Daten von zwei experimentellen Durchläufen erfasst werden. Diese umfassten jeweils 26 Stunden eines Testprogramms, bestehend aus initial zehn leckagefreien Stunden, gefolgt von je zwei Stunden der über Drosseln simulierten Leckagen – aufeinanderfolgend an jedem der acht Ventile (siehe Abbildung 3). Die Anlage arbeitete mit einem Betriebsdruck von 6 bar; die Drosseln für die Simulation der Leckagen waren auf 3 Liter pro Minute bei diesem Druck eingestellt. Im Vergleich zum Gesamtdurchfluss lagen die simulierten Leckage somit grob geschätzt im Bereich von 1%.
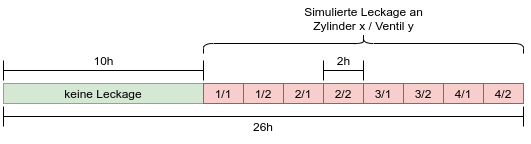
Abbildung 3: Leckagezustand während des stereotypen zeitlichen Ablaufs der beiden Testprogramme.
Anschließend begann die Arbeit des Data Science Teams der AIM. Beide Datensätze wurden auf Herz und Nieren überprüft. Dabei konnten die Experten die positive Auswirkung der Optimierungen auf die Netzwerkdynamik bestätigen. Dann rückte die Stunde der Wahrheit näher – ohne weitere Anpassungen wurde das Verfahren zur Erkennung und Verortung von Leckagen mit den Daten gefüttert. Das Verfahren verwendet dabei lediglich die Steuersignale der Zylinder sowie den zentral gemessenen Gesamtdurchfluss an Druckluft. Anhand eines leckagefreien Zeitabschnitts wurde das Verfahren kalibriert. Anschließend konnten Aussagen bzgl. des Leckagezustands entlang anderer Zeitabschnitte für jedes der acht Ventile getroffen werden. Im Rahmen der verwendeten Konfiguration passierte dies alle 100 Sekunden und bezog sich auf die jeweils vorausgehenden sechs Minuten.
Die Ergebnisse
Erfreulicherweise können wir berichten, dass AIMs Methode mit einer Trefferquote von durchschnittlich 98% die Leckagen für jedes Ventil erfolgreich erkennen und korrekt zuordnen konnte (siehe Abbildungen 4 und 5). Wie die Ergebnisse zeigen, funktioniert dies auch über beide Datensätze hinweg (bei einem Abstand von ca. 14 Tagen) ohne eine erkennbare Beeinträchtigung der Genauigkeit. Mit einer geeigneten nachgelagerten Bewertung der vom Verfahren als positiv erkannten Zeitabschnitte ist es darüber hinaus möglich, ohne großen Aufwand sämtliche Fehlalarme zu verhindern und im Rahmen der Testdaten zu einer Erkennungsrate von 100% zu gelangen.
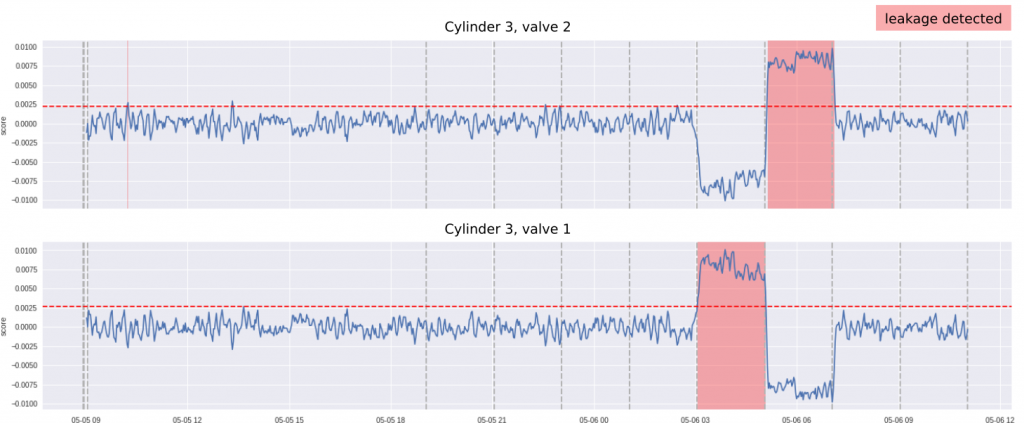
Abbildung 5: Vergleich der Vorhersagen (Prediction) gegenüber den tatsächlichen Leckagen (Actual) von Zylinder 3 pro Ventil (Valve). Ergebnisse sind normiert auf die tatsächliche Anzahl (Actual) von zugehörigen Zeitabschnitten. Blau hinterlegte Zahlen: Vom Verfahren korrekt zugeordnete Zeitabschnitte. Weiß hinterlegte Zahlen: Vom Modell falsch zugeordnete Zeitabschnitte.
Abbildung 4: Die vom Verfahren errechnete Bewertung (score) am Beispiel von Zylinder 3 für den Zeitbereich der Testdaten (Zweiter Durchlauf des Testprogramms). Kalibriert wurde das Verfahren auf dem leckagefreien Zeitraum vom 14 Tage zuvor aufgenommenen ersten Durchlauf des Testprogramms. Rote, vertikale Balken: Überschreitet die Score das innerhalb der Kalibrierung bestimmte Niveau, wird eine Leackage angezeigt. Graue, vertikale Balken: Wechsel der experimentellen Bedingungen (Leckagezustand, vergleiche Abbildung 2).
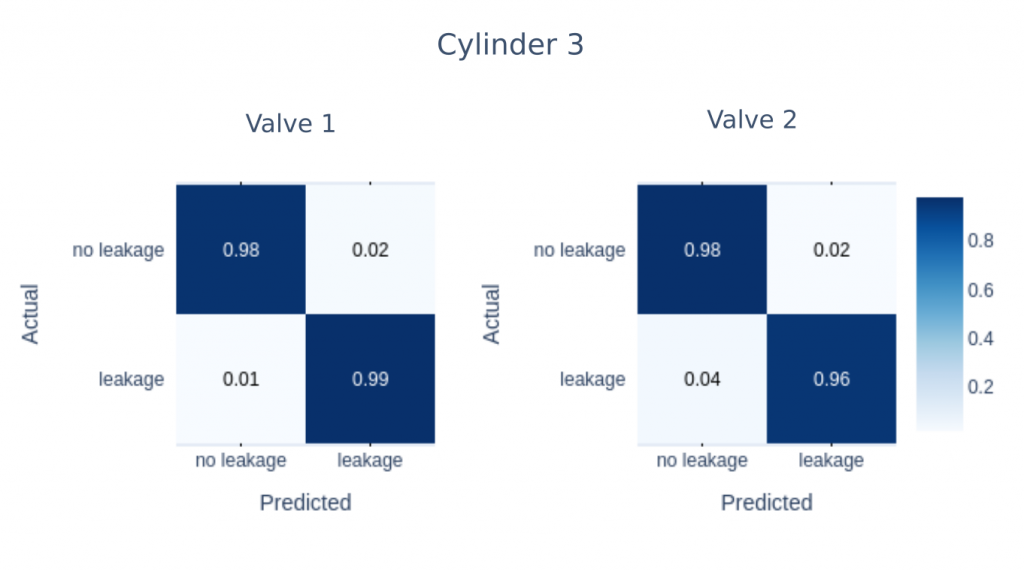
Einsatz im produktiven Betrieb
AIM geht davon aus, dass sich ihr Verfahren auch in produktiven Szenarien als ähnlich robust und genau herausstellen wird. Basierend auf den im Produktivbetrieb üblichen Schaltzyklen der Zylinder wird das Verfahren statistisch belastbare Aussagen innerhalb von wenigen Stunden liefern können. Entsprechend schnelle Reaktionszeiten für zielgerichtete Wartungsarbeiten werden somit zu einer spürbaren Reduktion von Kosten und Ressourcen führen. Zudem deuten die Analysen von AIM auf eine gute Generalisierungsfähigkeit über unterschiedliche Steuerprogramme hinweg. Daher freuen sie sich darauf, ihre KI-gestützte Leckage Lokalisierung schon bald in erste Anlagen beim Kunden integrieren zu können.
Nächster Schritt: Live-Demo der Leckageverortung
Ein offensichtlicher Vorteil des hoch getakteten Testprogramms liegt in der Möglichkeit, die Wirkungsweise des Verfahrens direkt vor Ort innerhalb von wenigen Minuten live demonstrieren zu können. Dank der produktiven Zusammenarbeit aller Beteiligten wurden bereits die nächsten Schritte hierfür eingeleitet. Entsprechend wird das derzeit offline betriebene Verfahren vor Ort installiert und die notwendigen Interaktionsmöglichkeiten geschaffen. Diese umfassen die gezielte Steuerung der Leckagen über eine Benutzeroberfläche sowie die Visualisierung der vom Verfahren getätigten Aussagen zum aktuellen Leckagezustand der Anlage.
Dr. Joachim Haenicke, AIM Data Scientists und Product Owner Smart Machines betont die gelungene Zusammenarbeit: „Wir freuen uns sehr über die erfolgreichen Ergebnisse und die reibungslose Zusammenarbeit mit unseren Kooperationspartnern bei Emerson und dem Fraunhofer IOSB-INA. Mit Blick auf die Corona-Inzidenz-Werte lässt uns auch diese positive Entwicklung der Rahmenbedingungen darauf hoffen, schon bald vor Ort die Anwendung des Verfahrens direkt erleben zu können. Wir können es kaum abwarten!“
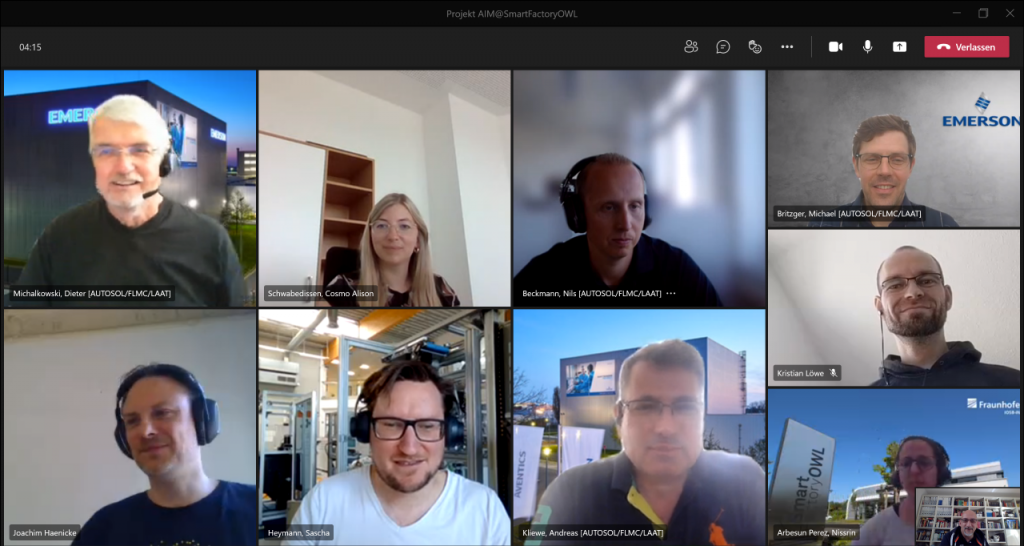
Abbildung 5: Gemeinsame Planung der nächsten Schritte.
Quelle: AIM