Assistance in manual assembly
through XTEND|assembly
By using the stationary system XTEND|assembly, users can be guided step-by-step through complex production processes. Relevant information of a production step is projected directly onto the workstation or workpiece in the form of texts, graphics or video sequences and can be operated with intuitive pointing and hand gestures. By displaying process-related data in the immediate vicinity of the work area, users are given the opportunity to perceive important information at any time while concentrating on their primary work tasks. In addition, the operating effort required is minimized, since no peripheral input devices are needed to interact with the system. 3D cameras around the workbench capture not only the users and their arm movements, but also the workspace and all objects in it, such as material boxes. In addition, tools that have previously been provided with simple markers are cost-effectively documented in use and screwdriving positions are automatically confirmed and recorded.
Contact
Prof. Dr. Dr. Dr. Carsten Röcker
Fraunhofer IOSB-INA
Campusallee 6 | D-32657 Lemgo
Intelligent assistance systems
Due to the expected increase in complexity in production, demographic change and increasingly shorter product life cycles, users will have to be increasingly supported by adaptive assistance systems in the future. The targeted use of assistance systems can both increase the flexibility of a system and guarantee individual support for employees. Thus a decisive competitive advantage can be achieved.
At Fraunhofer IOSB-INA, application-specific assistance systems are developed which, thanks to their modular structure, can be used in a variety of ways in production. The applications range from the guidance of unskilled workers, the support of employees in complex assembly processes up to the support of people with mental and physical disabilities to enable new perspectives in inclusive work.
The XTEND platform developed at Fraunhofer IOSB-INA combines, depending on the application, the advantages of different input and output systems and offers a modular assistance system to support different industrial activities. XTEND expands the physical working environment of the user with process-related digital (additional) information in the immediate vicinity of the work area. This enables employees to perceive important information at any time, for example with the aid of data glasses, projections or mobile devices, while at the same time concentrating on their primary work task. The focus here is on an adaptive user interface which, above all, expands the cognitive and physical possibilities of the employees and places their competence at the centre of a versatile production environment.
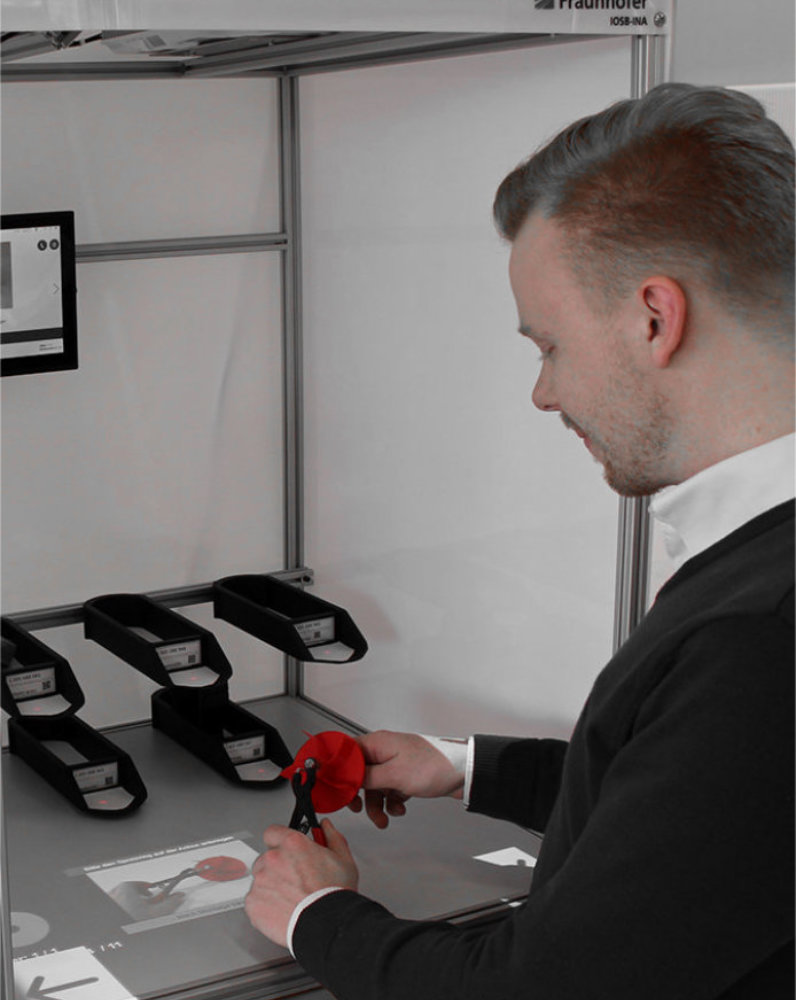
Context-based and mobile support through XTEND|mobile
XTEND|mobile enables improved machine and plant maintenance by superimposing and superimposing digital information into the work context via data glasses. With the help of the camera installed in the terminal device, the assistance system recognizes the environment of the respective work context. In this way, machine components relevant to the process can be visually identified. The gesture recognition built into the system can register user interaction with these components and thus offer adaptive and situation-dependent content. In addition, users can store digital information in the form of notes at strategically important points in the work scenario. This information can include work instructions, assembly support, or maintenance information. In this way, they can be retrieved, called up and updated at a later date in the same place with the help of the application.
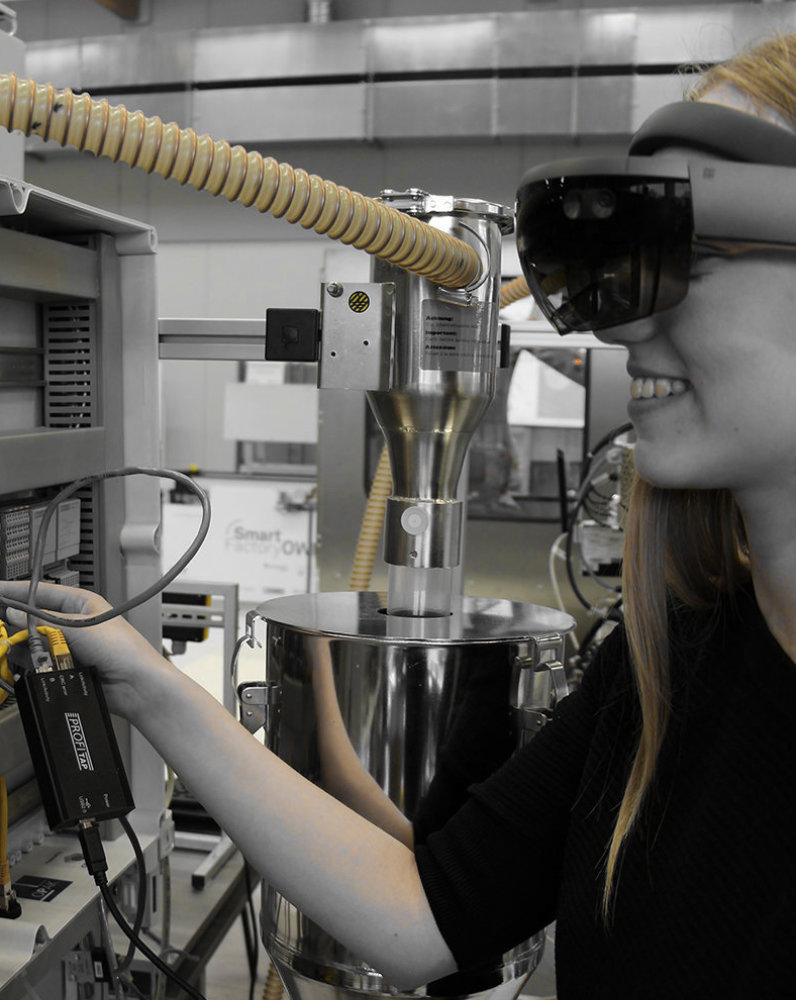
On-the-job qualification through XTEND|training
XTEND|training enables inexperienced employees to be trained in the areas of assembly, servicing and maintenance. The active support of the employees is provided by projection-based assembly support as well as tracking of the work steps carried out by hand and gesture recognition. In this way, on the one hand, the quality of the assembled products is to be increased and, on the other hand, the possibility is to be created of pointing out product peculiarities to employees in a more targeted manner in order to identify possible sources of error in advance. The assistance system depends on the individual needs and abilities of the employees and adapts the speed and content of the learning process accordingly with the help of intelligent algorithms. For example, the visual assembly assistance can be reduced during the learning process in order to avoid monotonous work procedures and to effectively support the employees during the process.
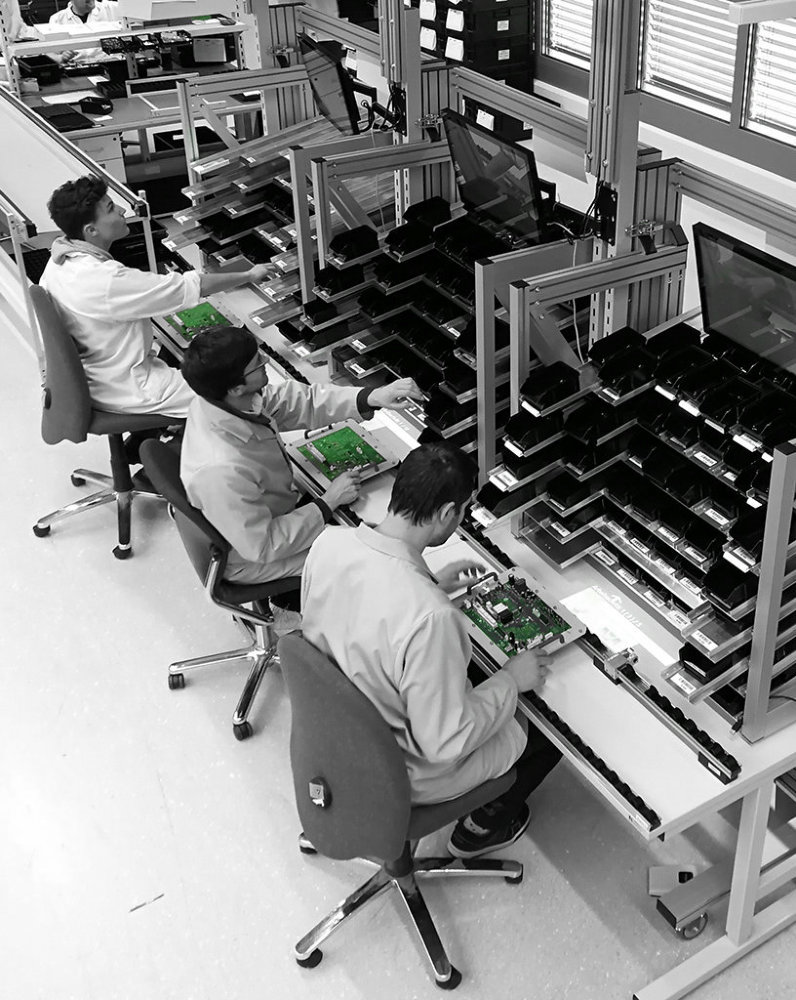
Cross-site assistance through XTEND|remoteSupport
For production distributed over different locations, the assistance system XTEND|remoteSupport relies on networked assistance that connects workstations regardless of location. For this purpose, the data exchange between the different components of the production system is implemented using common industry 4.0 standards such as Automation Markup Language (AutomationML) or OPC United Architecture (OPC UA). On this basis, a seamless data flow can be created and, through synergies, a broad usability of the system can be enabled. In addition, the standards support the cooperative work between two workstations: In an Augmented Reality-based video conferencing mode, remote fitters can connect to each other if necessary and act from different camera perspectives in the working environment of the foreign assembly process. In an innovative interaction mode, they can actively highlight areas in the observed workspace for targeted instruction.
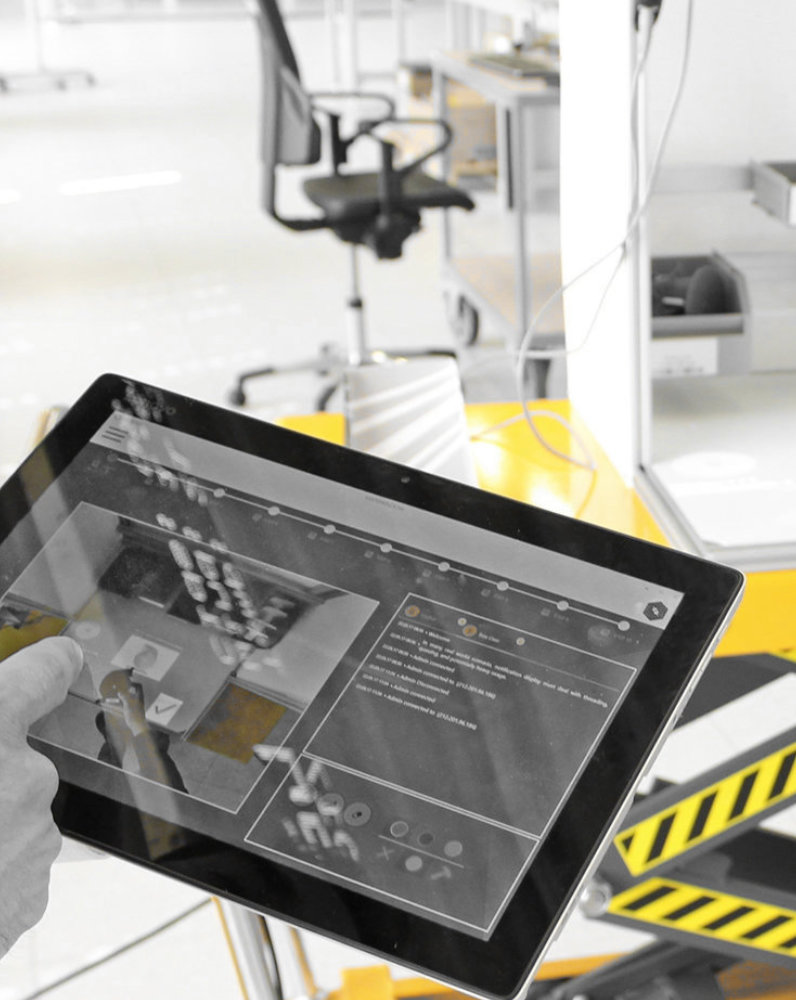